Table of Contents
When it comes to mining, especially the deep, dark depths of underground mining, there’s one piece of equipment that stands out as a true workhorse—the underground loader. Whether you’re a seasoned miner or just someone curious about how things work in the bowels of the earth, understanding underground loaders is crucial. In this blog, we’re going to dig into (pun intended) the world of underground loaders, covering their history, the different types, and why they are indispensable in mining operations.
1. The History of Underground Loaders: From Rocker Shovels to Modern Machines
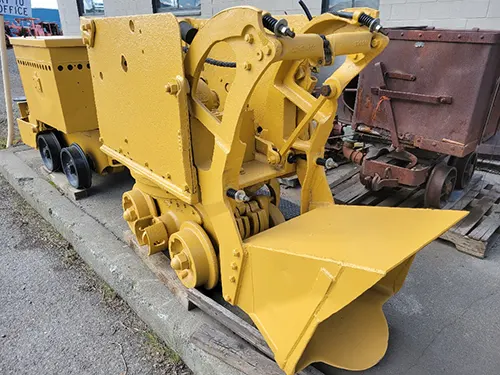
The history of underground loaders is as rich as the ore they help to extract. One of the earliest underground loaders was the Eimco 12B rocker shovel, a machine that still finds use in some mines today. Imagine operating a piece of equipment so robust and reliable that it’s been around longer than your grandpa’s first pair of work boots! The Eimco 12B was a game-changer in its time, making the grueling task of mucking (that’s mining lingo for moving broken rock) a lot more efficient.
Fast forward to today, and underground loaders have evolved into sophisticated machines with cutting-edge technology. These days, the focus isn’t just on moving rock but doing so with maximum efficiency and safety. Remote control operation? Check. Heavily armored to withstand the harsh underground environment? Double check.
2. The Big Three: Types of Underground Loaders
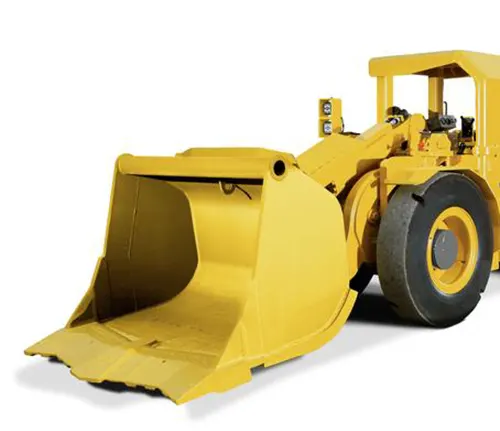
When it comes to underground loaders, not all are created equal. There are three main classes of underground loaders, each with its own set of strengths and ideal applications:
Conventional Front-End Loaders: These are the big boys, often used in large room-and-pillar mines where there’s plenty of space to maneuver. Picture a Komatsu WA600 or a CAT 990G doing its thing in a Kentucky limestone mine, moving massive amounts of material like it’s no big deal. However, they’re not as durable as loaders specifically designed for underground work, and remote control operation? Forget about it.
LHDs (Load-Haul-Dump): Now, these are the real underground heroes. Purpose-built for narrow, low-clearance environments, LHDs are the go-to for most underground mining operations. They’re tough, agile, and designed to take a beating. Most of them even come with remote control interfaces, so operators can stay out of harm’s way while the machine does the dirty work. And let’s not forget the ejector buckets, a nifty feature that allows these machines to load trucks even in tight spaces.
Pneumatic Loaders: If you’re looking for something a bit more old-school (and maybe a little risky), pneumatic loaders might be up your alley. These machines run on compressed air and are mostly found in smaller mines. The most common type, the overshot mucker, is known for literally throwing muck backward into an ore car or truck. Dangerous? Absolutely. But they’re cheap and get the job done, which is why some mines still use them today.
3. Why Underground Loaders Are Indispensable
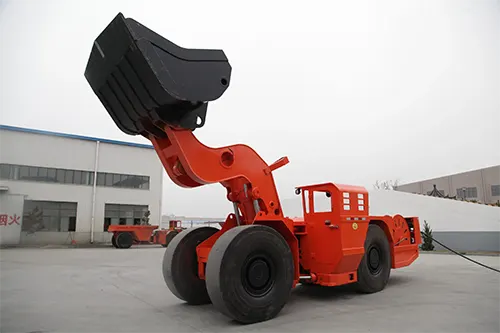
So, why are underground loaders such a big deal? It all comes down to efficiency, safety, and versatility. In an environment where every minute counts, these machines ensure that the mucking process is fast and effective. The ability to operate in tight spaces without sacrificing power makes them essential in many underground mining operations.
Safety is another crucial factor. With features like remote control operation, LHDs allow operators to stay at a safe distance from hazardous areas, reducing the risk of accidents. And in a world where safety regulations are becoming increasingly stringent, having reliable equipment like underground loaders is more important than ever.
4. The Modern-Day Underground Loader: What to Expect
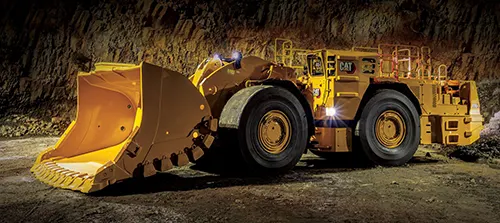
Today’s underground loaders are marvels of engineering. Take a stroll through a modern mine, and you’ll likely see LHDs equipped with state-of-the-art technology. These machines are not only built to last but are also designed with the operator’s comfort in mind. Many come with ergonomic seating, advanced control systems, and even climate control to ensure that operators can work efficiently in harsh conditions.
In terms of durability, today’s loaders are built with heavy-duty steel plates and minimal plastic components, ensuring they can handle the rough-and-tumble environment of underground mining. And if you’re looking to save on operational costs, modern LHDs are also designed to be energy-efficient, reducing fuel consumption without compromising performance.
5. The Future of Underground Loaders: Automation and Beyond
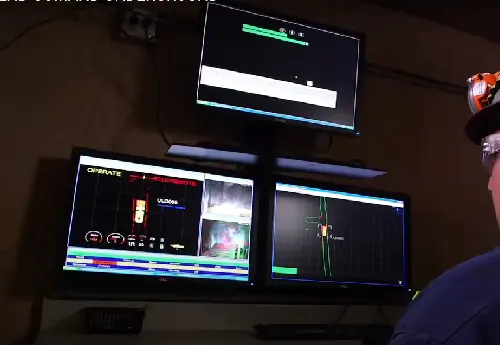
The future of underground loaders is looking brighter than ever. With advancements in automation, we’re seeing more and more mining companies investing in fully automated loaders. Imagine a fleet of loaders working 24/7 without the need for breaks, all controlled from a central command center located miles away from the mine. This is not science fiction—it’s the future of underground mining.
Automation not only increases efficiency but also enhances safety by removing operators from potentially dangerous environments. As technology continues to evolve, we can expect underground loaders to become even more sophisticated, with AI-driven systems that can adapt to changing mining conditions on the fly.
Conclusion: Why Underground Loaders Are the Backbone of Mining Operations
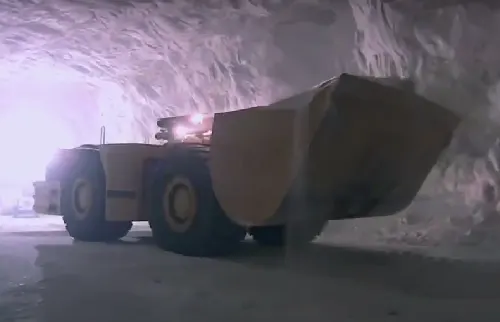
Underground loaders may not be the stars of the mining world, but they’re definitely the backbone. Without them, the process of moving ore from the mine to the surface would be slow, labor-intensive, and dangerous. Whether it’s the reliable old Eimco 12B or a cutting-edge LHD, these machines play a crucial role in keeping mining operations running smoothly.
So, the next time you think about the mining industry, spare a thought for the underground loaders. They’re the unsung heroes that make it all possible.