Table of Contents
What is a powershift transmission? Why do you need a transmission at all? Well, it’s because an engine all by itself just won’t cut the mustard. The work we do with construction machines requires high speeds and low speeds, but enough torque at any speed.
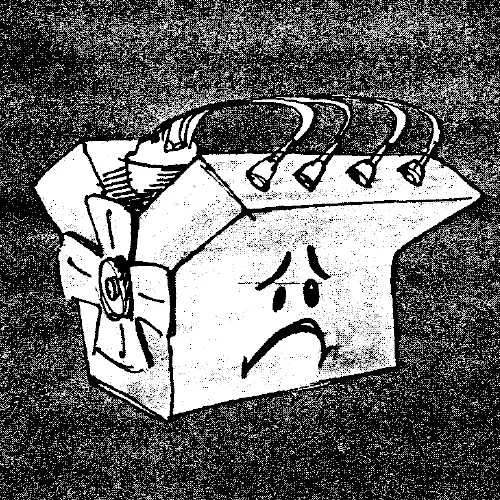
The problem is that an engine really only puts out within a certain R.P.M. range.
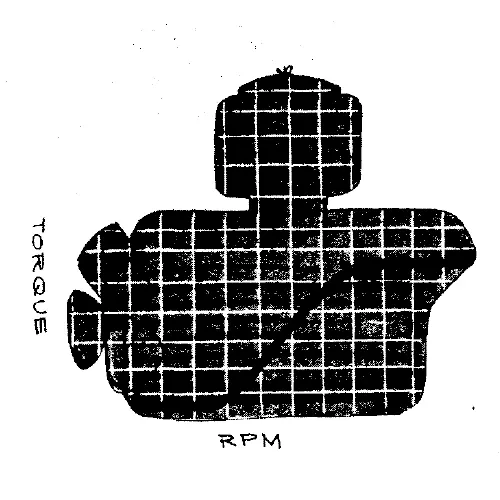
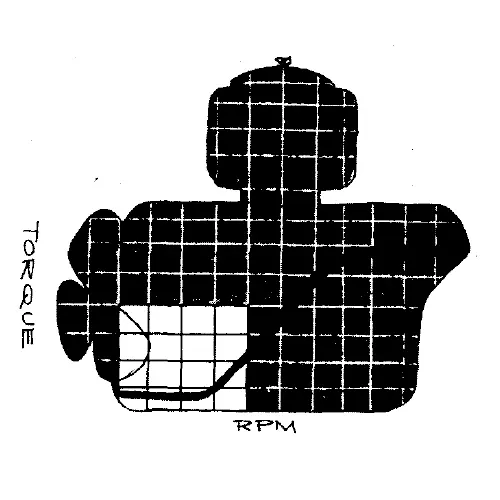
Torque and R.P.M.
Run it slower than that range and it just doesn’t have the power. It might be possible to build an engine with plenty of torque over a wide R.P.M. range, but it would have to be so big that you’d need King Kong to operate it.
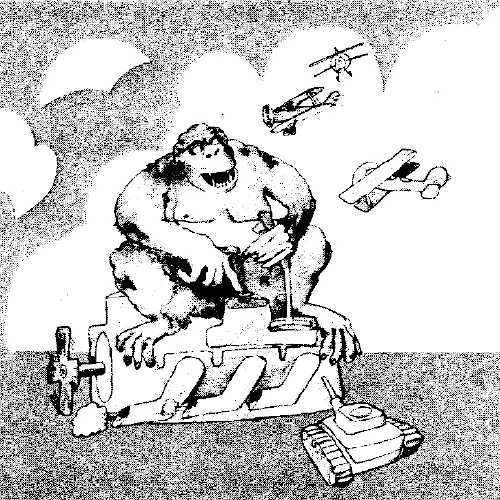
So we use a transmission to keep that engine at the proper R.P.M. while we’re doing work that would otherwise be too slow or too fast for that engine. The transmission gives us the flexibility to do a variety of speeds.
So, what is a powershift transmission?
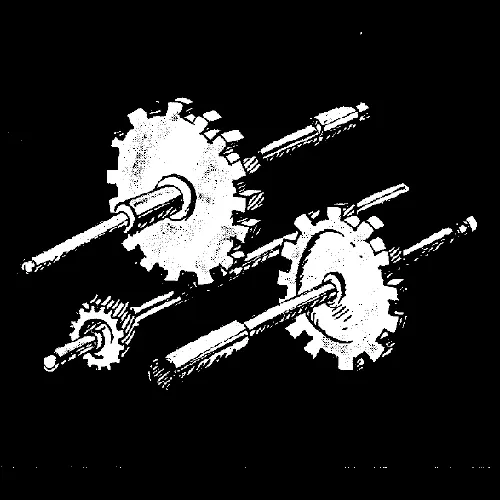
It’s a set of gears and shafts which transmit energy from the engine to the driving wheels of a machine.
And this transmission gives you three big pluses.
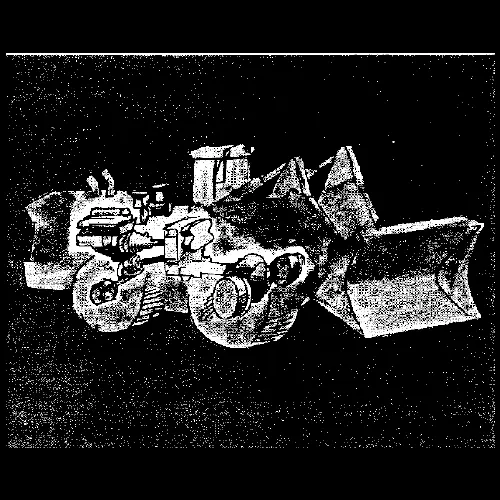
First, the machine doesn’t always have to be rolling while the engine is running. You put that transmission in neutral and the engine can turn over even though the machine is standing still.
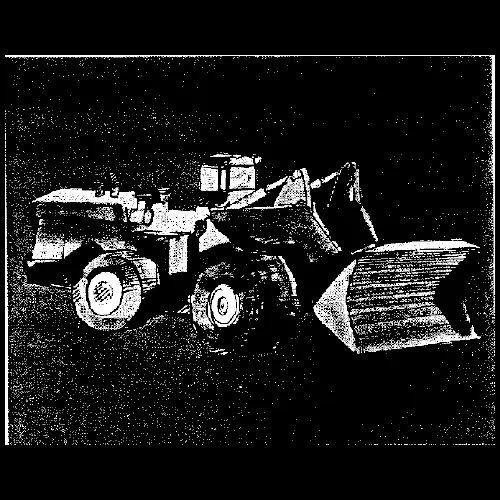
Second, when you need a lot of power and a lot of torque like for going up a steep grade or pushing something heavy you have a high gear ratio in the transmission. This high gear ratio is commonly called low gear.
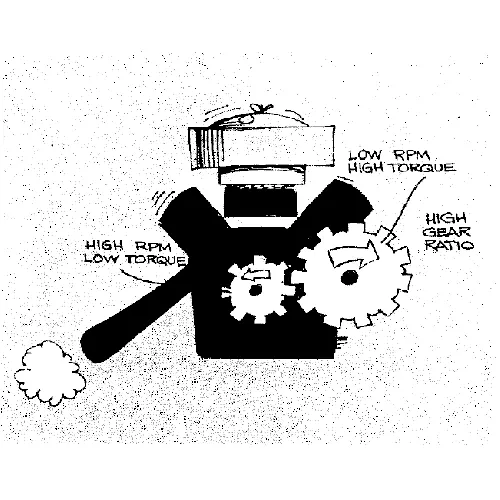
And, when you need speed, you have a low gear ratio or high gear.
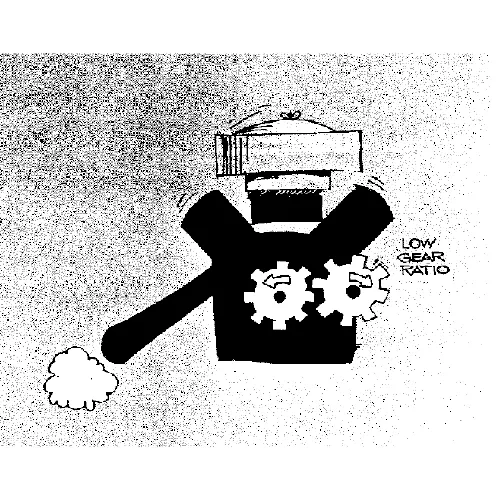
Types of Transmission
There are all kinds of transmissions. There are the sliding gear and synchromesh types which use sliding gears and a mechanical friction clutch.
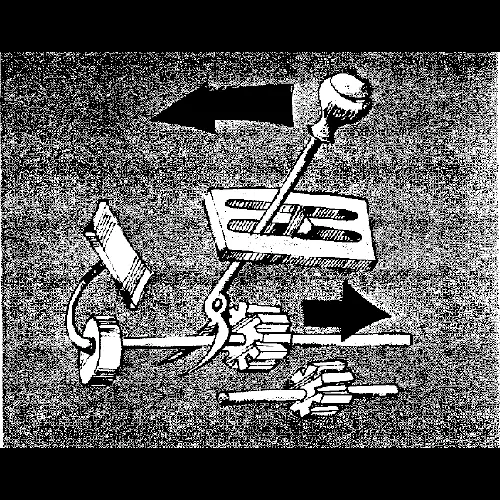
And there is the automatic transmission, which uses hydraulics to actuate clutch bands. In this transmission, the gears don’t slide but are always meshed. A governor control senses the speed and load and directs the hydraulic oil to whichever clutch bands give the best gear ratio for the work being done.
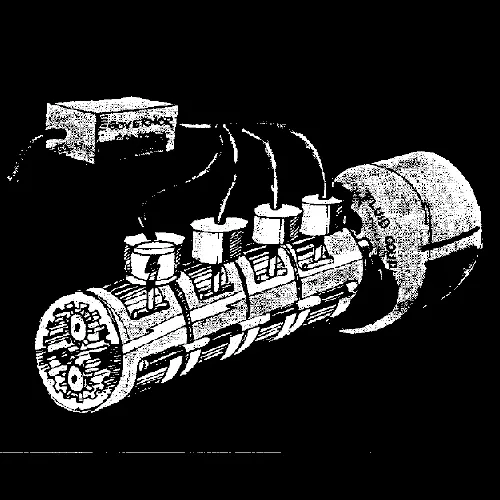
To smooth out the process, this type of transmission gets its power from a fluid coupling.
Clutch Discs
Yantai Prestone Powershift Transmissions are like an automatic transmission, in that the gears are constantly meshed, and the power comes from a torque converter. But instead of clutch bands, a powershift transmission has clutch discs which engage the gears and these hydraulically operated clutches are not activated by some sort of mechanical governor, but are activated by the operator himself.
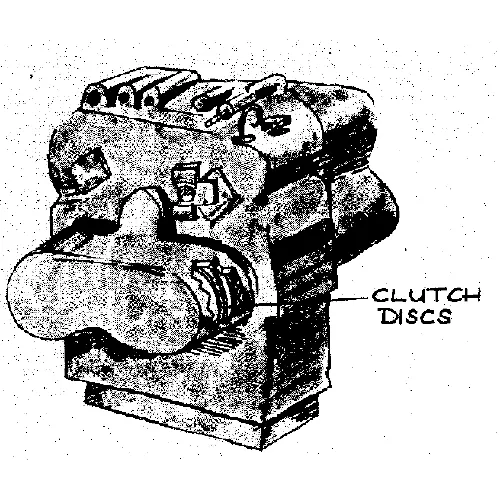
As you can see, if you understand these hydraulic disc clutches, you will have a pretty good understanding of the powershift transmission in general.
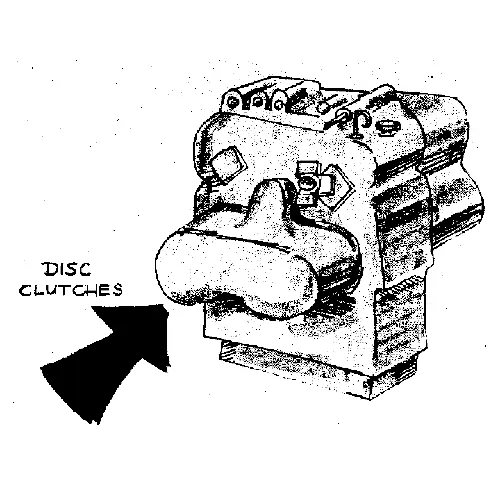
Let’s build one of these clutches from the ground up and you’ll see some clever engineering. Imagine a shaft with grooves cut in its surface and a disc with tongues that fit the grooves.
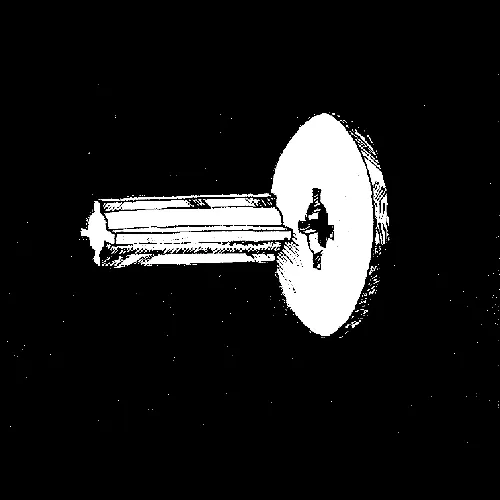
As you can see, a disc like this could slide back and forth in the grooves but could not rotate independently of the shaft.
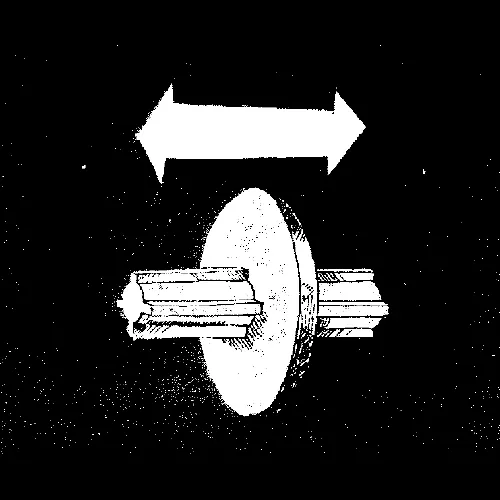
Now imagine a cylinder with grooves cut in its inside surface and a disc with tongues to slide in these grooves.
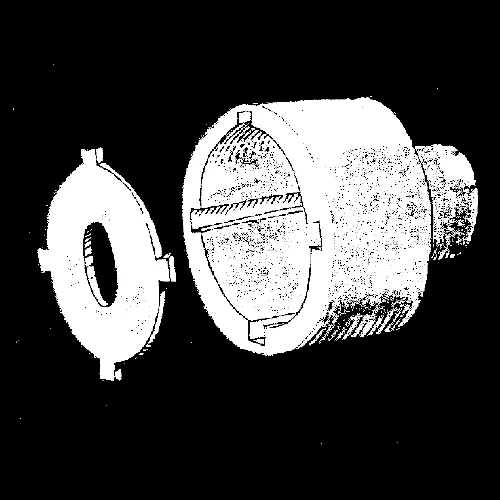
Once again, the disc can slide back and forth but because of the tongue in groove arrangement the disc cannot rotate independently of the cylinder.
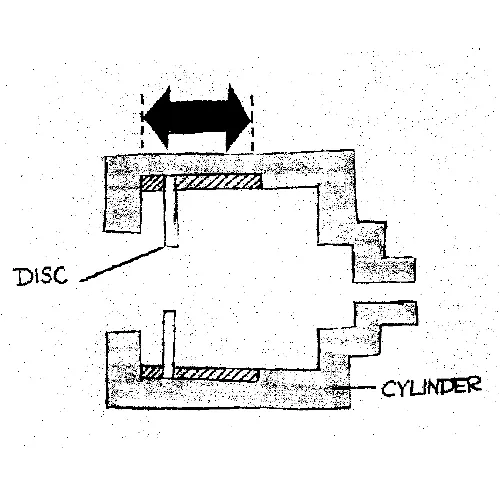
If you were to take the grooved shaft and place it within the grooved cylinder and alternate discs, so that one disc is tongued to the cylinder while the adjacent one is tongued to the shaft, you would have the beginnings of a clutch.
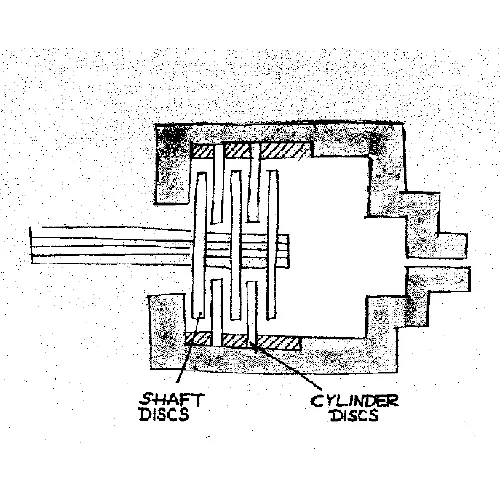
All of the discs in this mechanism can slide back and forth, but some discs turn only with the cylinder while others turn only with the shaft.
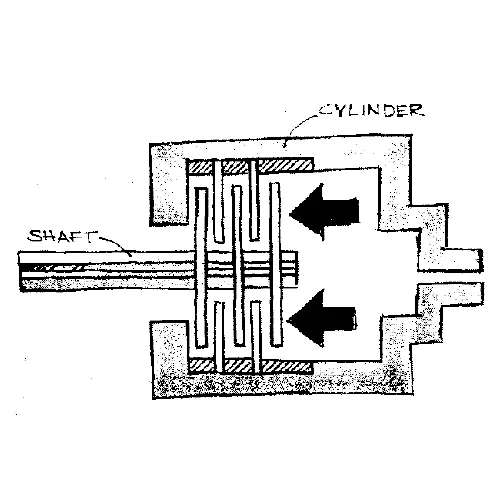
Hydraulics
If a piston is installed at one end, and a path is provided for high pressure oil, then the mechanism is completed. Imagine that the cylinder is turning and the shaft is not. If the oil forces the piston against the discs, the discs press together forming a sandwich… a friction sandwich. The cylinders discs, pressing the discs on the shaft cause the whole mechanism to turn as one unit. And that’s how a hydraulic clutch works. Yantai Prestone has refined this basic mechanism and you should understand some these refinements. But before you can understand refinements, you need to know a few basic principles of hydraulics.
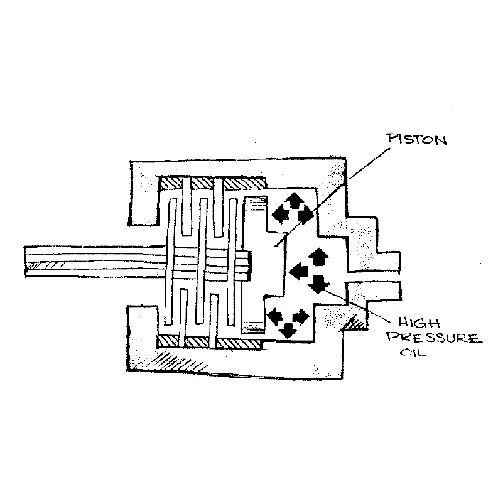
Here are two pistons in an oil filled cylinder. If you press down on piston A the oil transmits the pressure to all interior surfaces, but the only surface that gives in to that pressure is the bottom of the other piston, piston B.
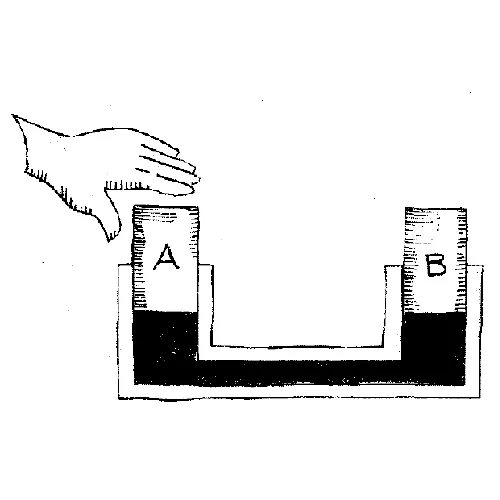
If both pistons are the same size, when you press down on piston A then piston B will rise out of the cylinder just as fast as A is depressed, and with just as much force.
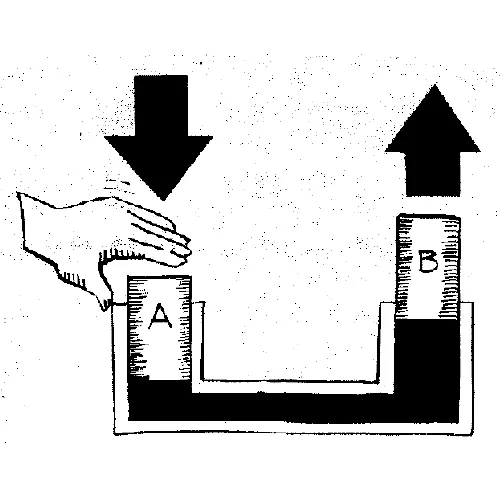
If piston B is smaller than piston A, when you press down on A, smaller piston B will rise out of the cylinder faster than A is depressed, but with less force. You’re trading speed for force.
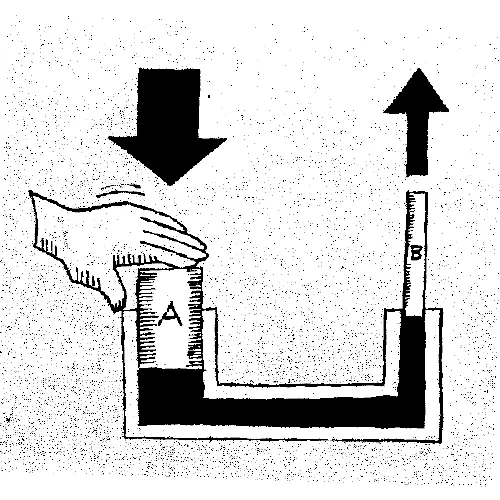
If the bottom surface of piston B is greater than piston A, when A is depressed, B will rise out of its cylinder more slowly than A is depressed… but with more force. Here you’re getting force in exchange for speed. You can see that the amount of piston surface determines how fast the piston moves and with how much force.
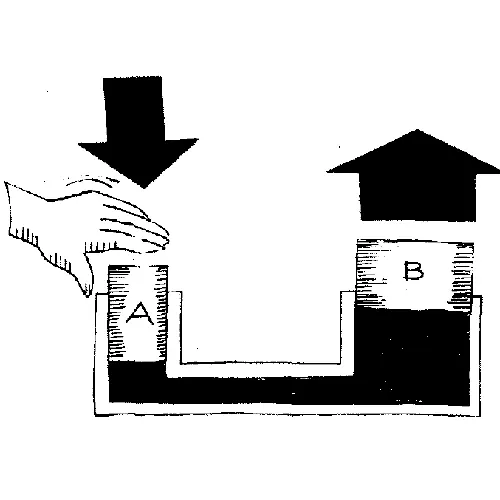
Now you’re ready to understand Yantai Prestone’s step piston. The piston within has two surfaces. When oil is directed to the piston, it initially acts only on the step piston’s small surface. The piston moves rapidly toward the discs, but without maximum force.
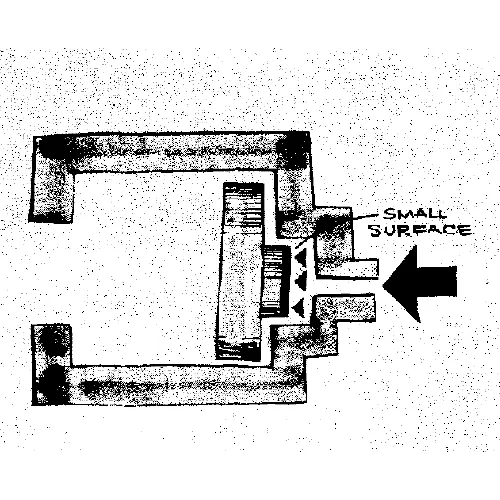
As the squeezed discs cause resistance to piston movement, the oil is forced around the edges of the small piston surface and begins to act on the additional surface, providing very great force. You will find that some clutches use a step up piston and some use a step down piston. Either way, the same principle is involved, the greater the surface the greater the force.
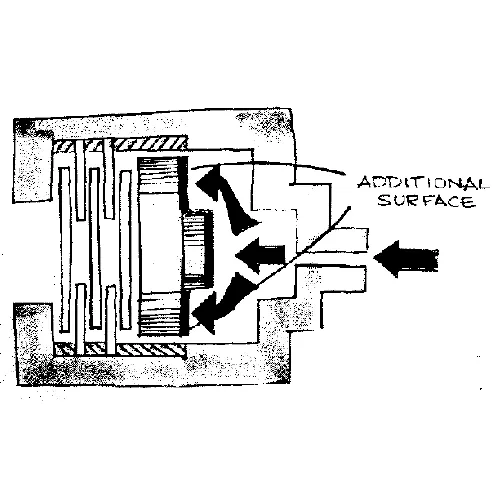
So the step piston design patented by Yantai Preston functions with clutch disc resistance to provide quick, smooth, and powerful application of force. So far we’ve only talked about applying the clutch. Let’s look at the way the clutch is released.
First, you have to release the oil pressure from behind the piston. This permits the piston return springs, which have been compressed by the moving piston, to push the piston away from the discs. But releasing the oil pressure doesn’t do the whole job. Some of the oil can escape back through the inlet passage.

Centrifugal Force
But because the drum is spinning rapidly, the oil flows with centrifugal force toward the outside of the drum making escape through the central inlet passage difficult. But if centrifugal force causes the problem, then centrifugal force can solve the problem.
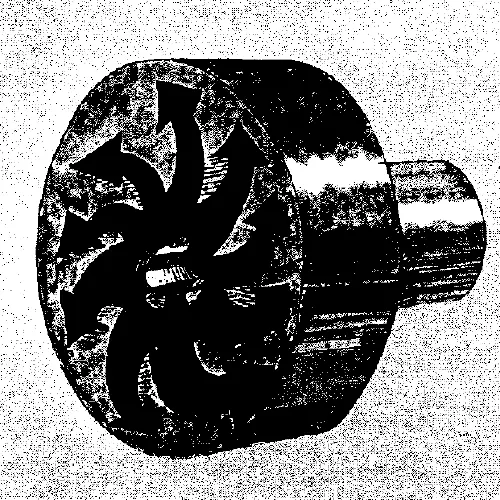
There is a check ball, fitted in a ramp at the outer edge of the drum.
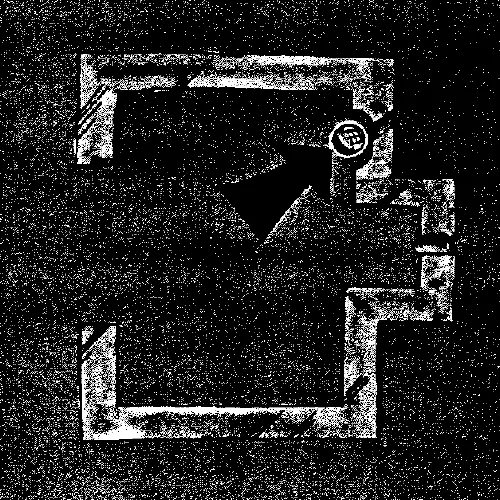
The ball rolls up the ramp because of centrifugal force, revealing an escape passage for the oil. This ball permits quick release of the clutch.
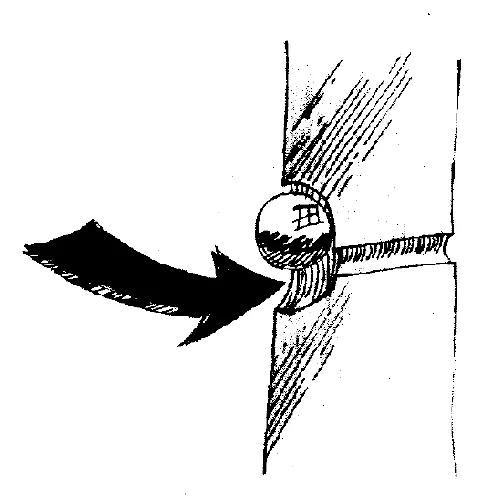
When the clutch is reapplied the high pressure of the oil forces the check ball into the neck of the escape passage preventing a loss in pressure.
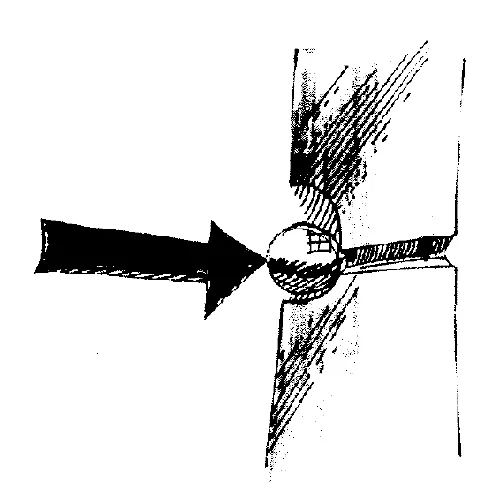
Components
So now you know about a couple of refinements Yantai-Prestone has engineered into the hydraulic clutch of a Powershift Transmission: the Step Piston, and the Ball Check Valve. But up till now you’ve been looking at a very simplified diagram of the clutch.
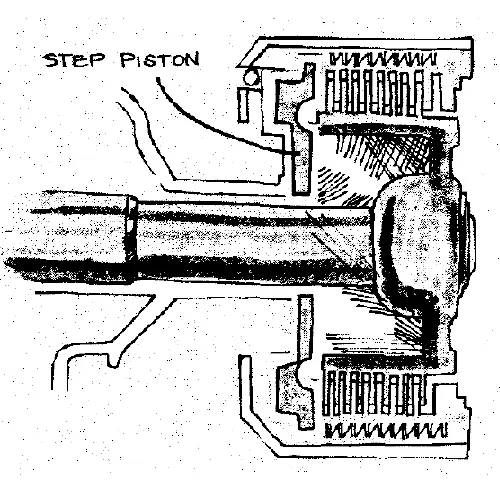
Here is a diagram to give you a better idea of what the real thing looks like.
The small and large surfaces of the step piston.
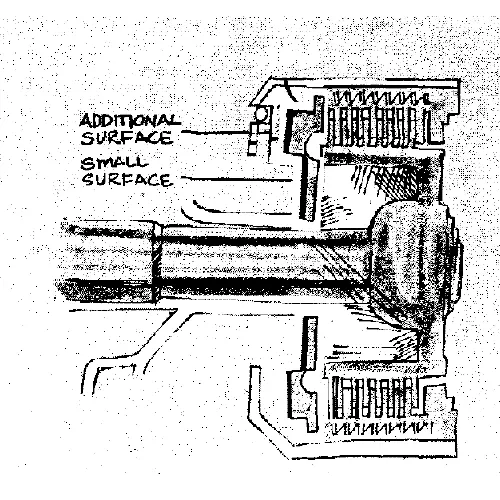
The discs –
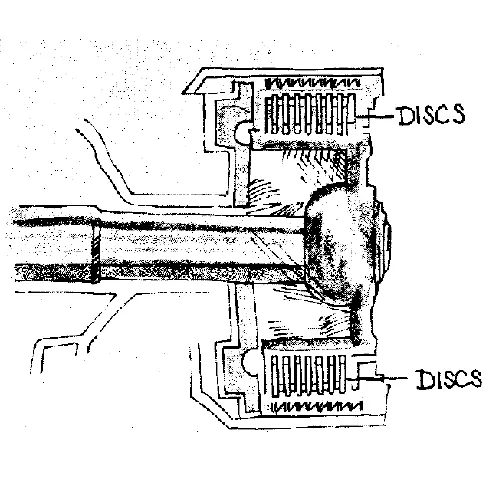
The piston return springs –
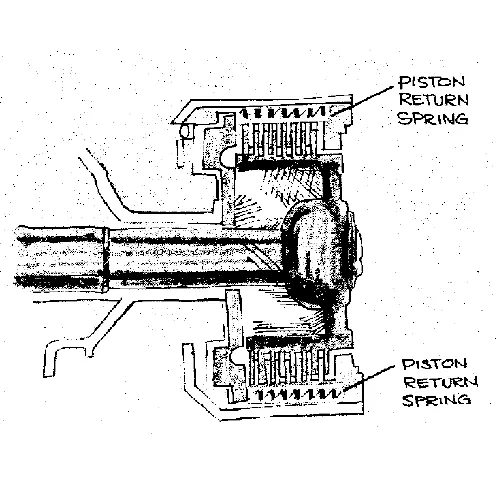
The inlet passage –
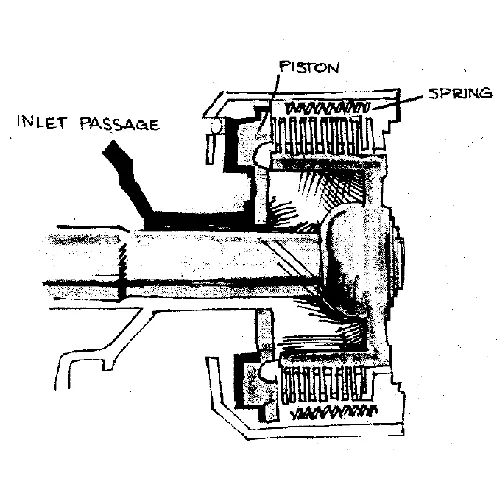
And the check ball escape passage.
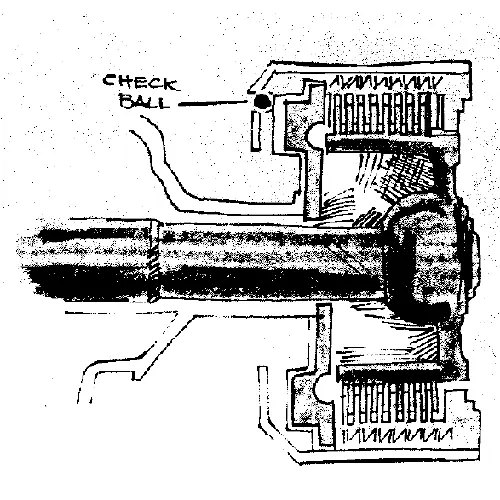
Here is a review of how the oil activates the clutch. High pressure oil is sent through the oil inlet passage forcing the piston into the discs and compressing the piston return springs.
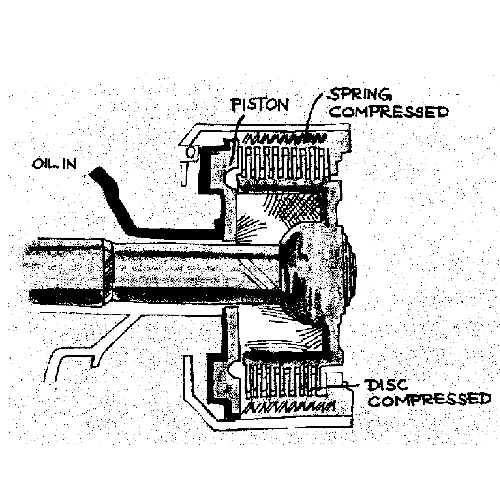
When pressure is released oil escapes back out the inlet passage, but also through the centrifugally operated check ball valve.
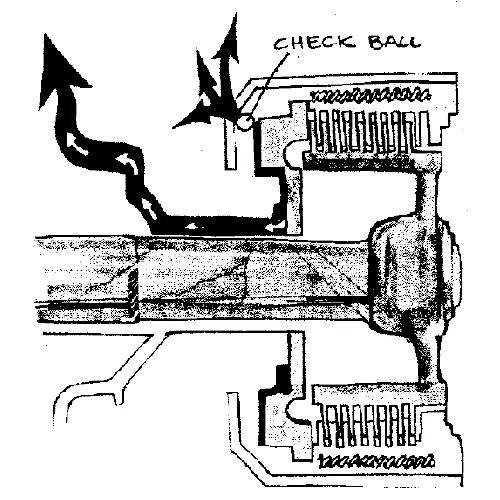
What is a Powershift Transmission?
A power shift transmission is nothing more than a series of these clutches which lock gears and shafts together to select various gear ratios or neutral. This Powershift Transmission has one clutch for each of the four speeds, plus one clutch for forward mode, and another for reverse. So a four speed transmission has a total of six hydraulic clutches. And anytime the vehicle is moving, two of the clutches will be engaged: either forward or reverse clutch and one of the four speed clutches.
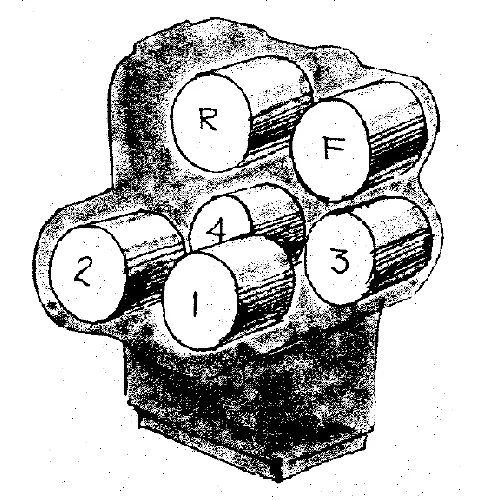
These clutches are activated through a device called the transmission control valve, which you will find mounted on top of the transmission case. This control valve does two things – it controls the amount of oil pressure to the clutches, and, it permits or prevents oil flow to the various clutches.
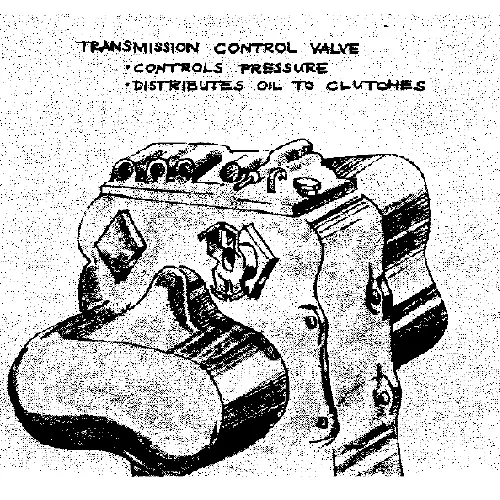
Kind of like traffic cop sending oil down one path and stopping it from travelling down another path. First let’s talk about how the valve regulates pressure.
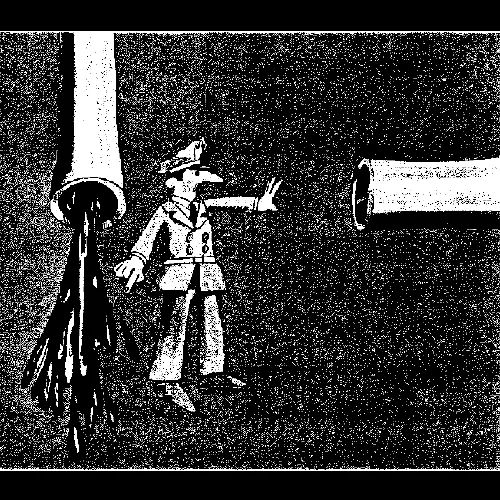
Oil is pumped in the valve by a gear type pump, sometimes called the converter charge pump. But the clutches operate best only within a limited pressure range.
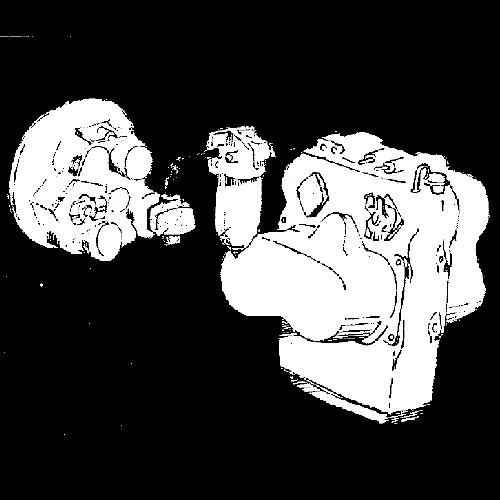
The pressure regulator valve consists of a hardened valve spool operating in a closely fitted bore. Oil entering the transmission from the charge pump must pass through the regulator valve. After passing through the valve, it will apply a speed clutch and stop. When oil flow is stopped at the clutch, pressure builds and oil flows through a passage behind the spool forcing the spool to move against the spring. As the spool shifts, it opens a port which allows the excess oil to charge the torque converter. This all happens within a fraction of a second.
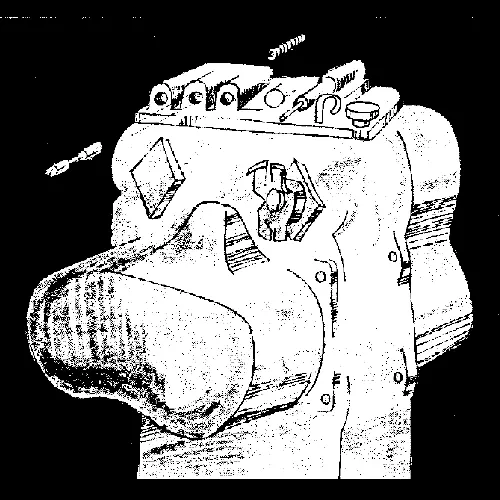
The spring which is holding tension against the spool is what regulates clutch pressure in the transmission.
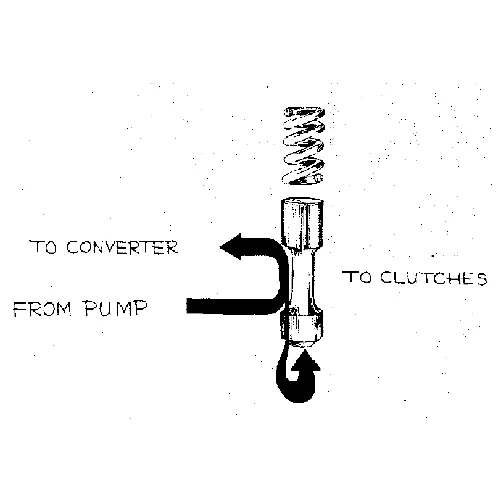
Very similar devices are used to activate the various clutches.
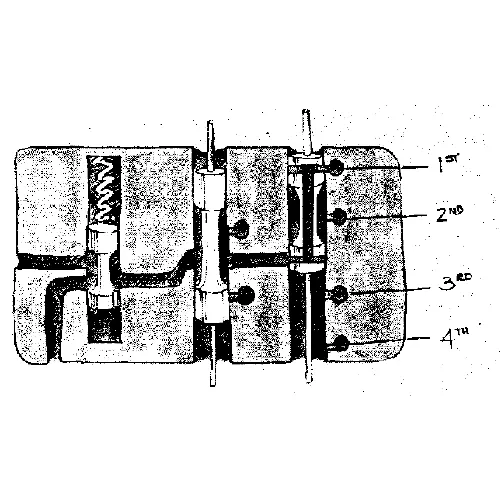
After oil passes the pressure regulator spool, it flows to the forward/reverse spool. When the spool is in this position, the forward clutch is activated.
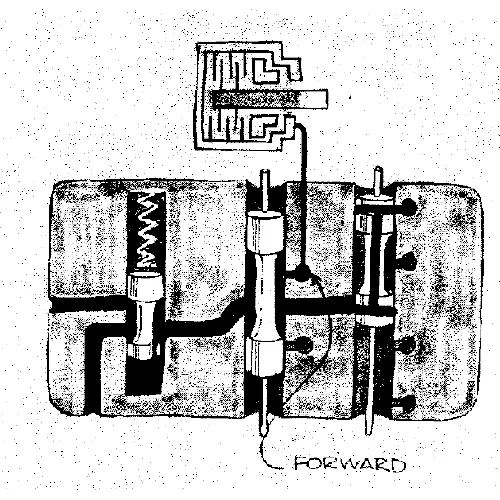
In this position the reverse clutch is activated.
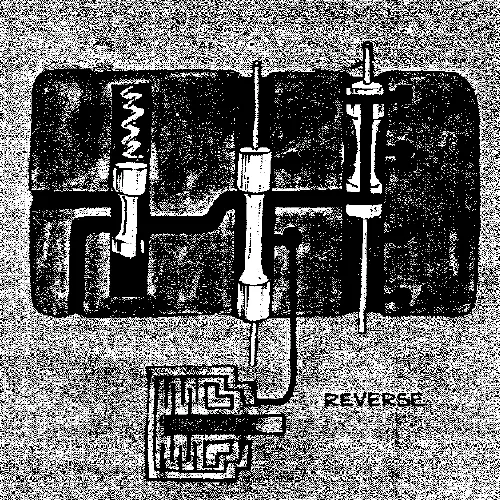
This position gives you neutral.
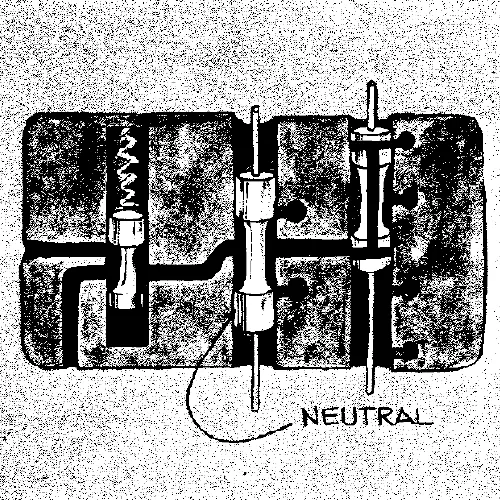
Right next door is the spool which gives you first, second, third, or fourth.
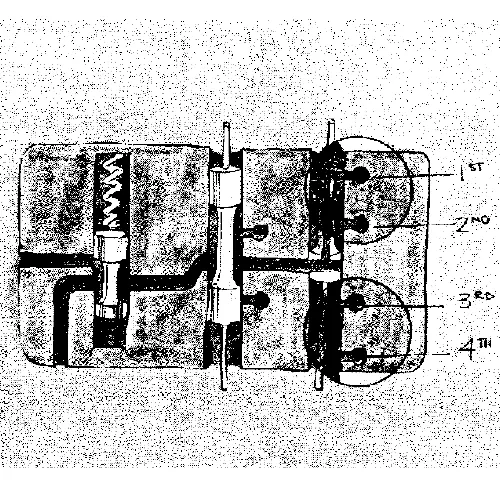
First….
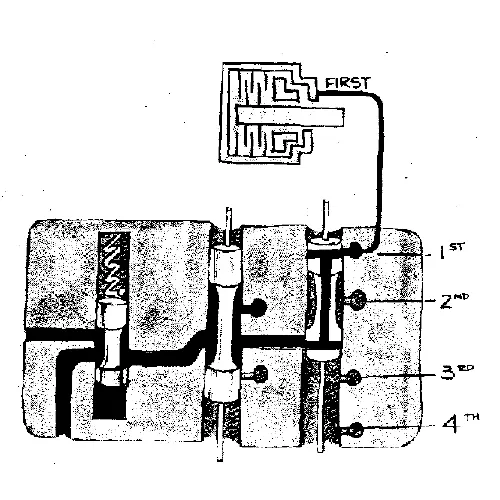
Second….
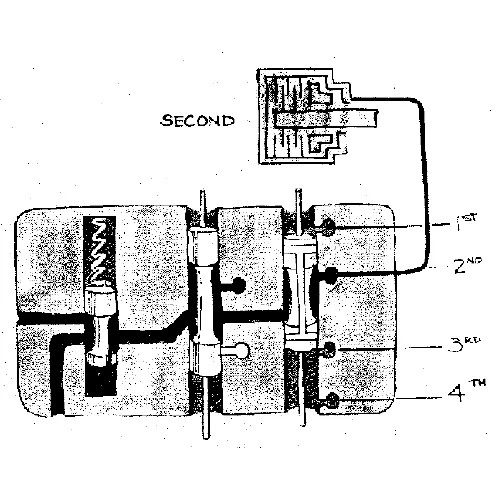
Third…..
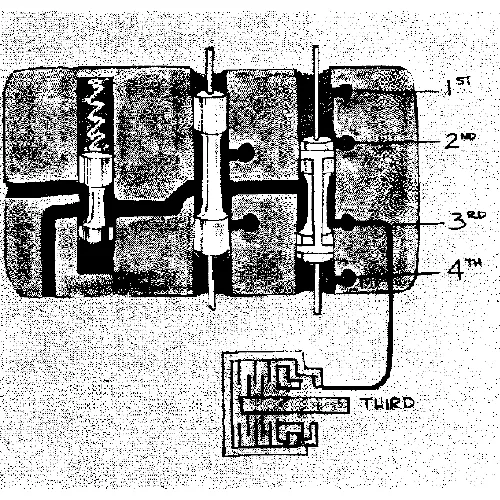
Or fourth…. And because the forward reverse spool is independent of the speed selection spool, you can have any of these speeds in reverse as well as in forward.
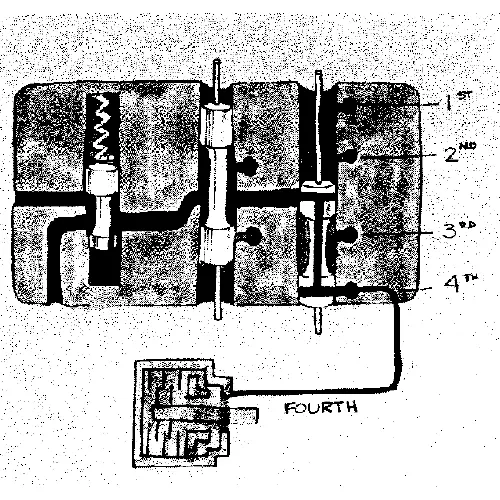
So you can see that there are basically three spools involved in the transmission control valve:
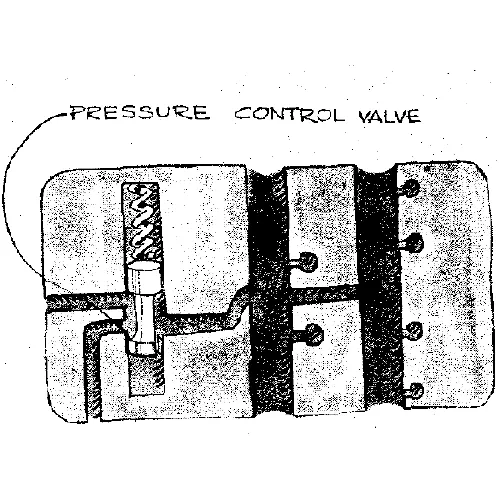
First the spool that regulates pressure,
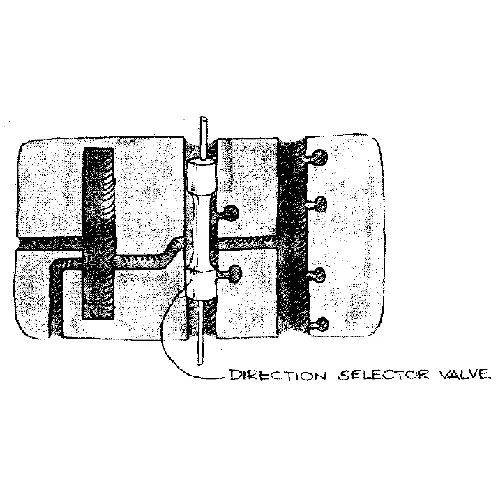
The one that gives you forward or reverse,
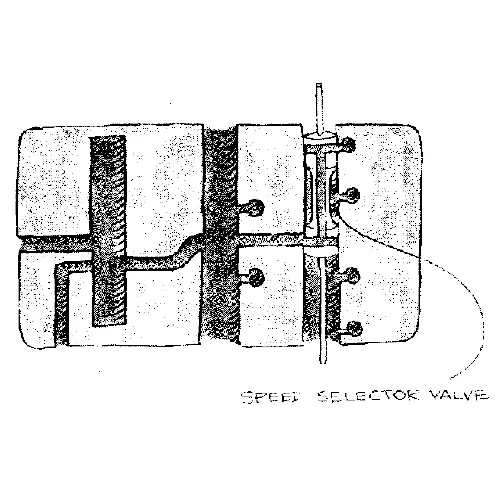
And the one that gives you speed selection.
You’ll find more detailed power flow diagrams for each powershift transmission in its manual.
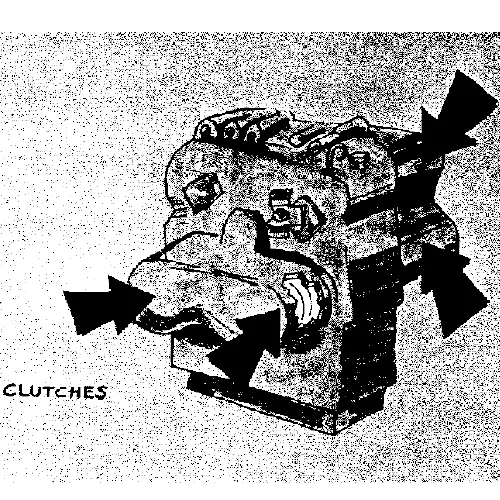
Well… that’s about it. What is a powershift transmission? A powershift transmission is nothing more than a series of clutches which lock gears and shafts together to select various gear ratios and forward or reverse mode…. And this selection is accomplished through the transmission control valve which sends oil to whichever clutches are selected by the operator.
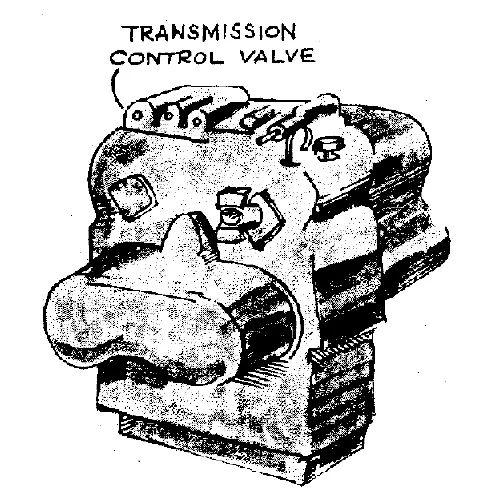