Table of Contents
LHDs have firmly established themselves as one of the most crucial and powerful assets in the underground mining industry. These remarkable heavy-duty machines are engineered to deliver maximum performance and efficiency, revolutionizing the way mining operations are carried out. Over the past several decades, the landscape of LHD technology has been continuously evolving, with a significant focus on embracing greener and more sustainable solutions. Let’s delve deeper into the world of LHDs, exploring their diverse types and uncovering the secrets behind their dominance in the underground mining realm.
History of LHD Machines
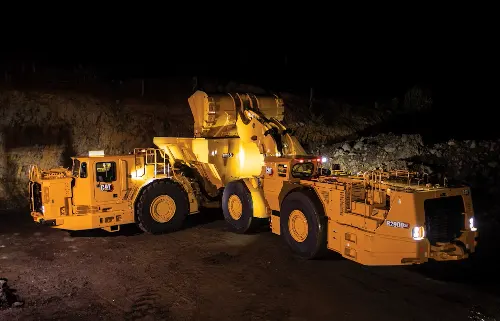
The concept of LHDs emerged in the mid-20th century as a response to the limitations of manual labor in underground mining. Early LHDs were basic adaptations of surface loaders, with limited capacities and simple designs.
The 1960s – 1970s brought technological advancements like more powerful engines, refined hydraulic systems, and better operator cabs with basic safety features.
In the 1980s – 1990s, LHDs became more specialized, with increased payloads, improved fuel efficiency, and enhanced operator comfort and safety features.
Since the 2000s, due to environmental concerns, the shift towards hybrid and electric LHDs began, along with the integration of automation and remote-control technologies, aiming for reduced emissions, quieter operation, and safer, more efficient mining.
Introduction to LHDs: Unveiling Their Core Functionality
LHD, or “Load Haul & Dump” machines, are a specialized breed of loaders that bear similarities to the traditional front-end loaders. However, they have carved out a unique niche in underground mining operations. Their primary role is to safely and efficiently load and transport hard rock and other materials between various sites within the mining complex. With a productivity-centric design, LHDs have found their way into over 75 percent of the world’s underground metal mines.
Despite having relatively slower travel speeds compared to conventional front-end loaders, they pack a punch with up to 50 percent increased loading capacity in a more compact and space-efficient form factor. Moreover, their smaller yet more robust engines contribute to better emissions control, aligning with the industry’s growing environmental concerns.
Construction Details: Tailored for the Underground Terrain
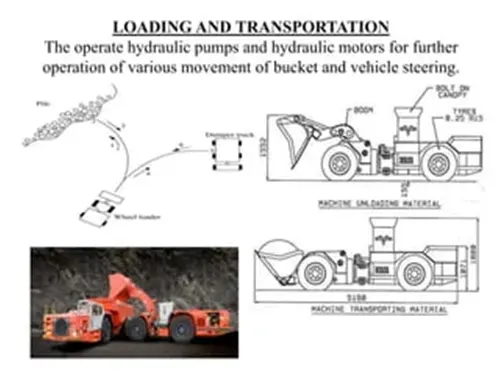
The construction of LHDs sets them apart from other front-end loaders. They possess a smaller footprint and a longer, narrower profile. This distinctive design not only ensures seamless adaptability to a wide range of working environments, from narrow tunnels to expansive stopes but also maximizes their loading potential. Although the elongated and narrower shape may slightly affect maneuverability, it more than compensates by enabling the machines to handle larger volumes of material. This enhanced loading capacity has made LHDs the go-to choice for underground mining projects, where space optimization and efficient material handling are of utmost importance.
Key Components of LHD Machines
The bucket is a vital part, varying in shape and size for different materials and applications, determining load capacity. Loader arms, hydraulically actuated, lift and lower the bucket with precision, their design affecting loading efficiency. The power train, with engine or electric motor and transmission, supplies the force for movement and hydraulic operations. Axles support the LHD and transfer power to wheels or tracks, which offer traction and stability. The hydraulic system powers component movements and includes pump, valves, cylinders, and hoses. The operator cabin provides a comfortable and safe space, equipped with ergonomic controls, good visibility, and safety features like ROPS and FOPS, along with creature comforts and performance monitors.
Productivity: The Driving Force Behind LHD Success
LHDs are synonymous with enhanced work cycle times. Their smooth operation, combined with a superior traction system, not only boosts overall productivity but also leads to reduced operation and maintenance costs. The compact yet powerful engines in LHDs offer the dual benefits of reduced emissions and heat load, along with faster acceleration and decreased fuel consumption. These remarkable features have firmly positioned LHDs as productivity-oriented workhorses, capable of delivering outstanding performance in even the most challenging working conditions.
Leading manufacturers like Komatsu have further enhanced the productivity equation by introducing innovative features such as the SR Hybrid Drive. This state-of-the-art Switched Reluctance Hybrid Drive system is engineered to capture and recycle braking energy, resulting in higher fuel efficiency, shorter cycle times, and industry-leading acceleration.
Safety Considerations: Protecting the Operators at All Costs
Safety is a top priority in the design of LHDs. Most models are equipped with a comprehensive suite of enhanced safety features. These include redundant/failsafe braking systems, emergency stop mechanisms, and ROPS/FOPS (Rollover Protection Structure/Falling Object Protection Structure) certification for the operator’s cabin. Every aspect of the machine’s design, from platforms and steps to handrails and stairs, is meticulously crafted with operator safety in mind. Additionally, LHDs offer improved suspension systems, which not only minimize vibrations in rocky terrains but also ensure a smoother operation in harsh working environments, safeguarding the well-being of the operators and enhancing their overall work experience.
Reliability: Built to Withstand the Toughest Underground Challenges
The robust steel frames of LHDs serve as a shield against the wear and tear and impacts that are inevitable in the harsh underground mining conditions. These machines are engineered to endure the most extreme working environments, ensuring uninterrupted operation. Equipped with advanced hydraulic systems featuring piston pumps, LHDs enjoy cooler operation and extended service life. Many also incorporate a central automatic lubrication system, which keeps the critical joints of the machines well-lubricated, reducing the frequency of regular maintenance and minimizing disruptions to the mining process. This unwavering reliability is a cornerstone of LHDs’ success in the demanding underground mining industry.
Payload Capacity: Meeting Diverse Mining Requirements
LHDs come in a wide array of sizes, each offering distinct payload capacities. These typically range from 6,000 to 22,000 lbs. (2,700 to 10,000 kg) and can even reach an impressive 55,000 lbs. (25,000 kg). To cater to the specific needs of different underground mining operations, manufacturers offer a variety of bucket options. Bucket sizes span from 1 to 13 cubic yards (0.8 to 10 cubic meters), with bucket heights varying between 6 and 8.2 feet (1.8 and 2.5 meters). This extensive range of sizes and payload capacities allows LHDs to provide tailored solutions for every type of underground mining scenario, from small-scale operations to large-scale industrial mines.
Operator Cabins: A Haven of Comfort and Efficiency
In recent decades, significant strides have been made in enhancing operator comfort and safety within LHD cabins. Leading manufacturers have incorporated a host of comfort and safety features into their operator cabins, streamlining operations and bolstering productivity. Smart displays with integrated diagnostics and real-time operation metrics provide operators with valuable insights into the machine’s performance. Ergonomic controls, paired with optional features like air-suspended seats, ensure maximum comfort during long hours of operation, reducing operator fatigue and enhancing overall job satisfaction.
Automation: Transforming LHD Operations
LHDs have embraced the era of automation with open arms. Advanced automated controls have simplified complex tasks, allowing operators to execute them with a simple press of a button. This not only enables operators to focus more intently on the task at hand but also promotes greater productivity and smoother operation. Different manufacturers have introduced a variety of automation and intelligent control systems, all aimed at optimizing load cycles and maximizing efficiency. The availability of remote controls has further expanded the capabilities of LHDs, enabling them to operate safely in hazardous work environments where falling rocks pose a significant threat. Automated controls have thus emerged as a safer alternative to traditional human-operated LHDs in such challenging conditions.
Fuel-Based & Hybrid LHDs: The Path to a Greener Future
Traditionally, LHDs have relied on diesel fuel for their operation. However, in recent years, there has been a notable shift towards hybrid and electric-powered models. Hybrid LHDs, capable of operating on both diesel fuel and battery or electrical power, offer a host of benefits. They consume less fuel, resulting in lower emissions and a reduced carbon footprint compared to their conventional counterparts. The decreased emissions are accompanied by lower heat production, which in turn reduces the need and cost of ventilation in the mining environment.
With their positive environmental impact and a desirable combination of lower fuel consumption and higher efficiency, hybrid power is rapidly becoming the industry standard. Electric or battery-powered LHDs, in particular, offer smoother operation and lower long-term costs, with electric motors typically operating between 75 and 150 horsepower and a medium voltage of 380 to 550 volts.
Famous LHD Manufacturers
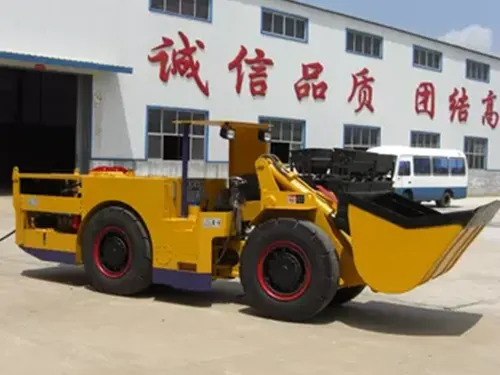
In the world of LHD (Load, Haul, Dump) manufacturing, several brands stand out. Caterpillar is a heavyweight, renowned for its rugged and productive LHDs. Their machines, with powerful engines and reliable drivetrains, can handle diverse mining demands. Komatsu focuses on operator comfort and safety, integrating modern tech like intelligent controls and hybrids. Sandvik’s LHDs are precise, often featuring automation and remote – control for efficient underground work. Atlas Copco optimizes productivity and cost – reduction, with features like good traction and ergonomic operator cabins. Epiroc, spun off from Atlas Copco, emphasizes energy – efficiency and high performance, providing reliable LHDs and solid after – sales support for global underground mining operations.
Conclusion: LHDs – The Future of Underground Mining
In conclusion, our exploration of LHDs has hopefully provided you with a comprehensive understanding of these remarkable machines and their pivotal role in the underground mining cycle. As the mining industry continues to evolve in response to technological advancements and global material demands, the focus on productivity and sustainability has never been stronger. Hybrid LHDs with increasing levels of automation are poised to play an even more significant role in the near future, shaping the way we extract and transport minerals from beneath the earth’s surface.