Table of Contents
Underground mining equipment is vital for the safe, efficient, and productive extraction of minerals and ores from beneath the Earth’s surface. These machines are engineered to withstand the harsh conditions of underground mining environments while ensuring optimal safety and performance. Let’s take a detailed look at the types of underground mining equipment, their role in the mining process, and what the future holds for this essential industry.
I. Types of Underground Mining Equipment
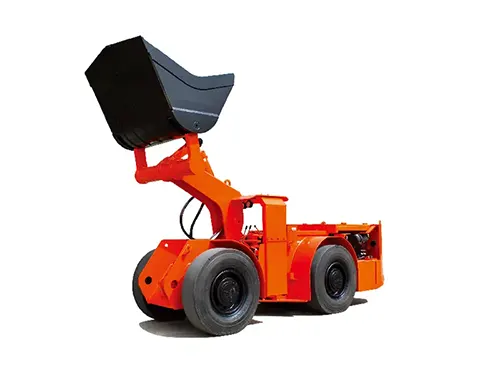
1. Drilling Machines
Drilling machines are the first step in underground mining operations, responsible for creating the holes needed for blasting or inserting support structures. There are various types of drilling machines depending on the size and scope of the operation.
– Hydraulic Jumbo Drills are the workhorses of large-scale drilling, capable of drilling multiple holes simultaneously with high precision and speed. These machines are typically used in tunneling operations where a wide area needs to be covered quickly.
– Face Drilling Rigs are another common type, used specifically for drilling into the rock face at the mining site. They are often used to create blast holes, which allow miners to break up large sections of rock for easier excavation.
Drilling machines are designed to be highly efficient and precise, reducing the amount of wasted material and increasing the speed of the mining process. The introduction of automated drilling systems further enhances productivity by allowing machines to operate continuously with minimal human intervention.
2. Loaders
Loaders are essential for moving the broken rock and ore from the mining face to trucks or conveyor belts for transportation out of the mine. These machines come in various sizes and configurations depending on the specific requirements of the mining operation.
– Scoop Loaders are smaller and more maneuverable, designed for use in narrow vein mining where space is limited. Their compact design allows them to navigate tight spaces while still being able to move significant amounts of material.
– Front-End Loaders are larger and more powerful, designed for use in larger underground mining operations. These loaders are capable of handling larger loads and are equipped with more powerful engines and hydraulic systems to maximize efficiency.
– LHD (Load-Haul-Dump) Machines are perhaps the most common type of loader used in underground mining. These versatile machines are designed to load, haul, and dump materials in a single operation, making them incredibly efficient in underground mining scenarios.
Loaders play a crucial role in reducing downtime and improving overall mining efficiency. The ability to quickly and efficiently move materials is essential to keeping the mining process running smoothly.
3. Haulage Equipment
Haulage equipment is designed to transport the mined material from the mining face to the surface or a processing plant. This equipment needs to be durable and powerful to handle the rough terrain and challenging conditions of underground mining.
– Underground Trucks are the backbone of underground mining haulage. These trucks are designed to carry heavy loads over long distances through rough, uneven terrain. Their rugged construction and powerful engines allow them to operate in harsh environments with minimal downtime.
– Rail Cars are another form of haulage used in some underground mining operations. These cars run on a fixed track and are ideal for transporting large volumes of material over longer distances.
– Conveyor Systems are often used in conjunction with other haulage equipment to continuously move material from one part of the mine to another. These systems are highly efficient and can handle large volumes of material with minimal energy consumption.
Articulated Dump Trucks, in particular, offer excellent maneuverability in tight underground spaces due to their flexible design. These trucks can carry heavy loads while navigating sharp turns and uneven ground, making them invaluable in underground mining operations.
4. Crushers and Mills
Crushers and mills are used to reduce the size of the mined ore to a manageable size for further processing. This is a crucial step in the mining process as it allows for more efficient separation of valuable minerals from the surrounding rock.
– Jaw Crushers are typically used for primary crushing, breaking down large pieces of rock into smaller, more manageable sizes.
– Cone Crushers are used for secondary and tertiary crushing, reducing the size of the material even further to prepare it for grinding or further processing.
– Ball Mills are used to grind the ore into a fine powder, which allows for easier extraction of valuable minerals. These mills are particularly effective at reducing ore to a size that is optimal for further processing and refining.
High-quality crushers and mills are essential for maximizing resource recovery and ensuring that as much valuable material as possible is extracted from the mined ore.
5. Ventilation Equipment
Ventilation systems are critical in underground mining operations, where fresh air is needed to maintain safe working conditions and remove harmful gases and dust.
– Axial Fans are large fans used to push fresh air into the mine and exhaust stale air. These fans are often reversible, allowing for the direction of airflow to be changed as needed depending on the requirements of the operation.
– Ducting Systems are used to direct airflow to different areas of the mine, ensuring that fresh air reaches all areas where workers are present.
– Air Filters are installed in the ventilation system to remove dust and other harmful particles from the air, ensuring that miners are breathing clean, safe air.
Ventilation equipment is essential not only for the safety of the workers but also for the smooth operation of the entire mining process. Proper ventilation can prevent accidents and minimize health risks associated with underground mining.
6. Support Equipment
Support equipment is used to ensure the structural integrity and safety of the underground tunnels and mining face.
– Roof Bolters are machines designed to install bolts into the roof and walls of the mine to prevent collapses. These machines are highly specialized and can quickly and efficiently install support bolts, improving the overall safety of the mining operation.
– Rock Bolts are used to reinforce the rock mass, helping to prevent collapses and improve the stability of the tunnels.
– Mesh is laid on the walls and roof of the mine to prevent loose rocks from falling, further enhancing the safety of the mining operation.
Support equipment is a critical component of underground mining, ensuring that the tunnels and mining face remain stable and safe for workers.
II. Importance of Underground Mining Equipment

1. Safety
Underground mining is inherently dangerous, but the use of modern mining equipment has significantly reduced the risks. Equipment such as ventilation systems, roof bolters, and support systems are designed to protect workers from cave-ins, gas leaks, and other hazards. For instance, safety cages on lifts and reliable ventilation systems ensure that miners are kept safe from falling debris and harmful gases.
2. Efficiency
The efficiency of underground mining equipment can make or break a mining operation. Advanced loaders, crushers, and haulage systems can handle more material in less time, reducing cycle times and increasing productivity. Automated systems, in particular, allow for continuous operation, reducing downtime and increasing overall efficiency.
3. Resource Recovery
High-quality mining equipment helps maximize resource recovery by ensuring that valuable minerals are effectively separated from waste rock. Modern crushers and mills can reduce the ore to a finer grade, increasing the extraction rate of valuable minerals. By improving the quality of the mined product, mining companies can increase profitability and reduce waste.
4. Environmental Impact
Many types of underground mining equipment are designed with environmental considerations in mind. Dust suppression systems on crushers and loaders reduce the amount of dust released into the environment, and energy-efficient machines help minimize the carbon footprint of mining operations. Some equipment is even designed to operate using electric power, reducing the reliance on fossil fuels.
III. Key Manufacturers and Brands
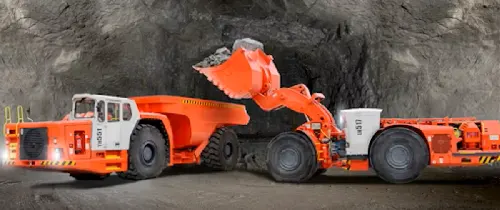
1. Sandvik
A global leader in mining equipment, Sandvik offers a comprehensive range of underground mining machinery, including advanced drilling systems, loaders, and trucks. Known for reliability and durability, their equipment is designed to perform in the harshest conditions, providing excellent results.
2. Caterpillar
Caterpillar’s wide range of underground mining equipment includes loaders, trucks, and graders. Their machines are known for their fuel efficiency, ease of maintenance, and robust construction. Caterpillar loaders, for example, offer powerful engines and large bucket capacities, ensuring optimal material handling in demanding underground environments.
3. Komatsu
Komatsu offers innovative underground mining equipment with advanced technologies aimed at reducing fuel consumption and operational costs. Their intelligent drilling systems adapt to rock conditions, improving efficiency and minimizing wear on the equipment.
4. Atlas Copco
Atlas Copco is another industry leader, offering a wide range of energy-efficient mining equipment such as compressors and ventilation systems. Their focus on sustainability and cost-effective operation makes them a popular choice for mining companies looking to reduce their environmental impact.
IV. Future Trends in Underground Mining Equipment
1. Automation and Robotics
Automation is rapidly changing the landscape of underground mining. Automated drilling rigs, loaders, and haulage trucks are already in use, increasing safety and operational efficiency by reducing the need for human labor in dangerous environments. Robotics will further enhance productivity by taking over tasks such as maintenance, inspection, and repair.
2. Digitalization and Connectivity
The integration of digital technologies such as IoT, sensors, and data analytics is allowing mining companies to monitor equipment performance and environmental conditions in real time. This connectivity enables better decision-making, reducing downtime and optimizing the use of resources.
3. Sustainability
As the industry faces growing environmental concerns, the demand for sustainable underground mining equipment continues to rise. Electric and hybrid vehicles are gaining popularity, offering reduced emissions and fuel consumption. Additionally, dust suppression systems and waste reduction technologies are helping to minimize the environmental impact of mining operations.
Related Links
CNR Underground Mining Equipment